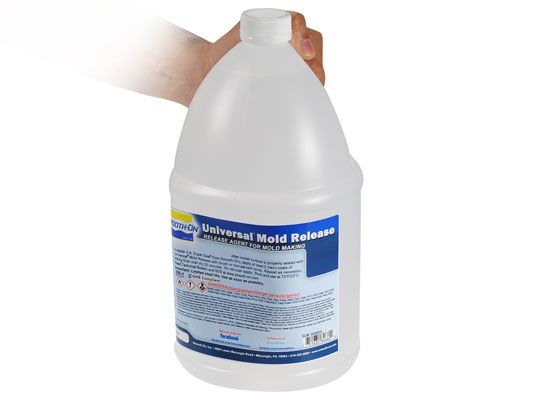
In the intricate world of manufacturing, where precision and efficiency are paramount, there exists a silent hero that plays a crucial role in the production process— the Mold Release Agent. Often overlooked, this unsung champion ensures the seamless release of products from molds, facilitating smoother operations and maintaining the integrity of the final output. In this blog post, we will delve into the significance of mold release agents, their applications, and how they contribute to enhancing manufacturing processes.
Understanding Mold Release Agents: Mold release agents, also known as mold release lubricants or demolding agents, are substances applied to molds to aid in the release of the molded product. These agents act as a barrier between the mold surface and the material being molded, preventing adhesion and facilitating easy separation. Mold release agents are employed in a myriad of industries, including automotive, aerospace, plastics, rubber, and composites, among others.
Key Functions of Mold Release Agents:
- Preventing Adhesion: One of the primary functions of mold release agents is to prevent the material being molded from sticking to the mold surface. This is crucial for maintaining the integrity of the molded product and ensuring a smooth release.
- Surface Protection: Mold release agents also play a role in protecting the surface of molds from wear and tear. Continuous use of molds without proper release agents can lead to damage and reduced lifespan.
- Improving Efficiency: By facilitating easy release, mold release agents contribute to enhanced efficiency in the manufacturing process. Reduced friction between the mold and the material being molded results in faster production cycles and increased throughput.
- Quality Assurance: The use of mold release agents helps maintain the quality of the molded products by preventing defects such as surface imperfections, cracks, or distortions that may occur during demolding.
Types of Mold Release Agents:
- Liquid Mold Release Agents: These are often applied as sprays and are suitable for a wide range of molding processes, including injection molding and rotational molding.
- Semi-Permanent Mold Release Agents: These agents provide longer-lasting protection and are typically used for more complex molding operations. They form a thin film on the mold surface and require periodic reapplication.
- Dry Film Mold Release Agents: These agents come in the form of powders or solid films and are often used in applications where liquid agents may be impractical.
Applications Across Industries:
- Automotive Industry: Mold release agents are extensively used in the production of various automotive components, including interior and exterior parts, tires, and rubber components.
- Plastics Industry: Injection molding and extrusion processes in the plastics industry benefit significantly from the use of mold release agents to ensure the smooth demolding of plastic products.
- Aerospace Industry: The aerospace sector relies on mold release agents for manufacturing composite materials used in aircraft components.
Conclusion: In the intricate dance of manufacturing, where precision and efficiency reign supreme, mold release agents emerge as the unsung heroes ensuring the smooth execution of processes. From preventing adhesion to preserving the integrity of molds, these agents contribute significantly to the quality and efficiency of various industries. As manufacturing technologies continue to evolve, so too will the role of mold release agents, solidifying their status as indispensable assets in the production landscape.